CLUB EY
Emilio Saavedra, Socio de Supply Chain & Operations en el área de Consulting, EY
Nº 36 – JULIO 2021
By:
Nuestra economía necesita reforzar su sector industrial y para lograrlo con competitividad es esencial aplicar una transformación digital profunda, a todos los niveles y escalable. De hecho, la única salida de la industria manufacturera europea es evolucionar hacia un modelo completamente digitalizado. Esta transformación digital permite alcanzar una capacidad productiva eficiente, aumentar la resiliencia ante cortes de suministro, proporcionar productos locales y generar un impacto positivo en el empleo de calidad y la economía regional. Analizamos los pilares de una transformación digital exitosa de las operaciones productivas y los errores a evitar para afrontar este reto con garantías de éxito.
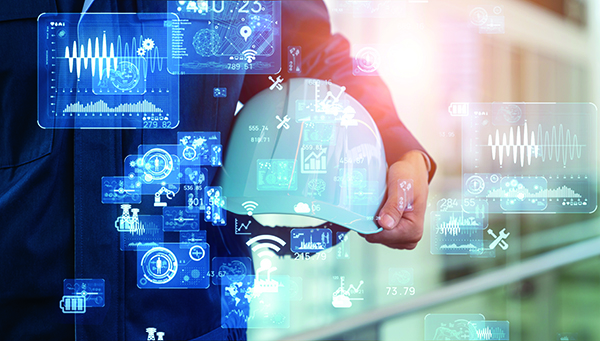
Durante los últimos treinta años hemos asistido a la pérdida progresiva de peso del sector industrial en la economía europea. Esta tendencia se acentúa todavía más en España, donde el peso del sector industrial en la economía ha sido tradicionalmente más bajo que la media europea.
En los últimos años esa diferencia se ha acrecentado. Si en el año 2000 el gap entre España y la UE respecto al peso del sector industrial en el PIB era de un punto porcentual (en Europa era del 17,3% y en España del 16,3%), en el 2019 esta diferencia se ha triplicado: Europa caía hasta un 14,4% y España a un 11,1%, según datos del Banco Mundial y la OCDE.
Por otra parte, a partir de los años 80, las economías asiáticas vieron despegar su sector manufacturero coincidiendo con la externalización de parte de la producción del mundo occidental hacia países que ofrecían producción a bajo coste. Esta tendencia se ha mantenido en el tiempo hasta crear una brecha de entre 10-15 ppp entre Europa y Asia en el peso de la fabricación en la economía, brecha que se sigue manteniendo hoy en día.
Esta externalización, que durante años ha aportado beneficios relevantes en competitividad en costes, a lo largo del tiempo ha mostrado desventajas que cuestionan este modelo:
- La competitividad en costes se está reduciendo por el incremento de los costes salariales. Por ejemplo, el salario medio en China prácticamente se ha triplicado en los últimos 10 años, según el National Bureau of Statistics of China. De hecho, China lleva años moviendo capacidad productiva desde la costa hacia el interior del país, donde los salarios son más contenidos, para proteger su statu quo.
- Pérdida de liderazgo estratégico en innovación. Por ejemplo, mientras Estados Unidos lidera el diseño de componentes electrónicos, Taiwán y Corea del Sur dominan la fabricación de chips, concentrando el 83% de la producción mundial de procesadores y el 70% de módulos de memoria.
Esta circunstancia se extiende a otros elementos clave de la economía del futuro, como las baterías de iones de litio. El primer país europeo del ranking de exportadores de baterías es Alemania, que figura en el 7º puesto, con un 5,6% del total. En los 6 primeros puestos, encontramos a 5 países asiáticos y a Estados Unidos, según datos de The World Factbook. - Riesgo de abastecimiento de suministros críticos. Un ejemplo reciente lo hemos visto durante la pandemia, con los problemas de suministro de respiradores o mascarillas. Desde la UE no fue posible responder en un principio al pico de demanda y hubo que recurrir a China para conseguir suministro. Y ya antes de la pandemia existían numerosos ejemplos en los que la externalización de la fabricación de principios activos a China o a India habían causado problemas de suministro con impacto en la fabricación de medicamentos.
- Cadenas de suministro complejas con pérdidas de agilidad y resiliencia. Volviendo al ejemplo de los chips, actualmente la alta tecnología está inmersa en una crisis de suministros. Por ejemplo, en la industria del automóvil la fluctuación en demanda y capacidad de fabricación por la pandemia, el desembarco del 5G y la progresiva digitalización han puesto en jaque a la industria, una situación que le está llevando a cuestionar un paradigma largamente instaurado en el sector como es el just-in-time.
Si a esto le añadimos la alta inversión y el tiempo necesarios para construir una planta de producción de chips (más de 24 meses) se entiende que la dependencia y debilidad de la industria europea en este campo pasen a convertirse en un aspecto estratégico. - Impacto social. Entre 2008 y 2018 se perdieron más de 370.000 puestos de empleo industrial en España. Numerosas empresas han salido del país o han reducido su actividad. El impacto en las comunidades locales afectadas puede llegar a ser irrecuperable debido al rol tractor que estas compañías jugaban en la economía.
- Preferencia de los consumidores. El reciente informe de EY “Deconstruyendo al consumidor en un entorno post-vacuna” indica que el precio, la disponibilidad del producto y el carácter saludable repiten como los atributos más valorados por el consumidor, aunque la crisis económica derivada de la pandemia ha hecho que el precio se coloque en primer lugar, aumentando en 9 puntos su valoración respecto a la anterior edición del informe. Esta circunstancia aumenta la presión sobre la eficiencia de la cadena de suministro.
Asimismo, continúa creciendo la importancia y valoración del origen local del producto, para generar un mayor impacto positivo en nuestra comunidad más cercana. Este factor refuerza la relocalización productiva en suelo europeo.
En esta nueva encuesta, los ciudadanos han valorado muy positivamente la disponibilidad de entrega con un aumento de 6 puntos, quedando patente la tendencia a visitar menos los establecimientos físicos y, por ende, alterando las redes logísticas que se balancean cada vez más desde un modelo B2B a un B2C.
Finalmente, el canal online sigue ganando peso. Consolida el acelerón experimentado durante la pandemia, en un escenario en el que la experiencia omnicanal es prácticamente obligatoria.
Por todo ello, tanto gobiernos como compañías están reflexionando y actuando en la dirección del retorno y refuerzo de la capacidad industrial. Además, esta tendencia ha sido bandera política en algunos procesos electorales de los últimos años, como en Estados Unidos, donde la estrategia arancelaria y de opinión han incentivado a las compañías a retornar producción del extranjero a suelo estadounidense.
España no es ajena a esta tendencia. De hecho, el gobierno actual incluía en su programa electoral objetivos específicos para aumentar el peso del sector industrial en el PIB: “Impulsaremos un Pacto de Estado por la Industria con participación de los agentes sociales, que buscará dar cumplimiento al objetivo de la UE de incrementar al menos hasta el 20% el peso de la industria en el conjunto del PIB español. Aprobaremos una nueva Ley de Industria, que adapte el marco regulatorio a los nuevos retos de digitalización y descarbonización, que actualice la regulación sobre calidad y seguridad industrial, y que reduzca las cargas administrativas favoreciendo una mayor coordinación con las Comunidades Autónomas y Corporaciones Locales”.
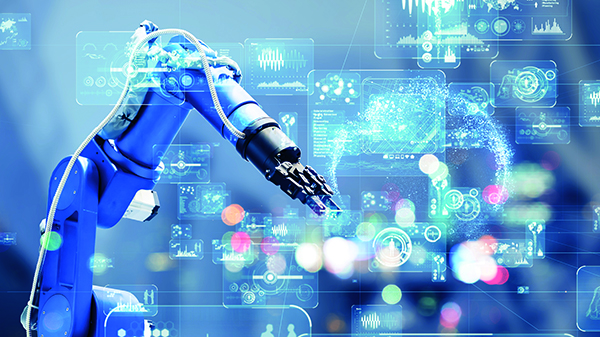
“En 10 años se ha triplicado la diferencia de peso del sector industrial: en Europa representa el 14,4% del PIB y en España el 11,1%”.
La dificultad de relocalizar fabricación en suelo europeo
Muchas compañías están revisando ya la arquitectura de sus cadenas de suministro, tanto a nivel de proveedores como de capacidades propias. El porcentaje de empresas que se platean el retorno varía en función de la industria, siendo aquellas que utilizan tecnologías avanzadas en sus procesos las más propensas al cambio. Equipamiento eléctrico, maquinaria, equipamiento de transporte, electrónica de consumo, químico y farmacéutico son los sectores más propensos a la relocalización. Otros sectores tienen un carácter más local, como la siderurgia, por lo que no suelen ser tan susceptibles a cambios de país, pero sí a procesos de racionalización, concentración y optimización.
Sin embargo, este retorno no se puede realizar a cualquier costa. Las compañías operan en un entorno global altamente competitivo por lo que cualquier movimiento debe realizarse bajo la premisa de, como mínimo, mantener la productividad y nivel de servicio actuales.
Por tanto, el sector se encuentra ante un reto complejo: ¿Cómo retornar o crear producción en suelo europeo de forma competitiva respecto a las economías emergentes? Si comparamos Europa y Asia es obvio que la diferencia del coste de la mano de obra no será la variable que proporcionará incrementos de productividad. Finalmente, desde el punto de vista de la digitalización y automatización de la fabricación, Europa en general cuenta con un nivel de robotización inferior a sus competidores asiáticos. Siguiendo con el ejemplo de Corea del Sur, el país asiático cuenta con 868 robots por cada 10.000 habitantes, mientras que Alemania (el alumno aventajado europeo) cuenta solo con 363. España por su parte cuenta con 191, menos de un 25% que Corea. Con este panorama está claro que la única salida que tiene la industria manufacturera europea es evolucionar su modelo hacia uno completamente digitalizado en el que tecnología y personas se refuercen entre sí para alcanzar niveles de productividad y agilidad excelentes.
La transformación digital, fácil de decir, pero difícil de hacer
Las compañías no son ajenas a todos estos retos y la práctica totalidad de las mismas están realizando o se plantean realizar programas de transformación digital y de excelencia operacional.
La última edición del estudio de EY “Global Capital Confidence Barometer” sigue situando la inversión en digitalización como la prioritaria y además acrecienta su relevancia.
Como contraposición a esta sensibilización del mundo empresarial nos encontramos, sin embargo, con el fracaso de los programas de transformación digital a la hora de cumplir las metas propuestas. Aproximadamente, un 70% de los programas fracasan, según un estudio elaborado por Mckinsey.
En realidad, esta problemática no es nueva. Existe una tendencia general en muchas compañías a no ser capaces de convertir los objetivos y planes definidos en sus reflexiones estratégicas en resultados en su cuenta de pérdidas y ganancias. Según un estudio publicado por Harvard Business Review, la mayoría de las estrategias solo consiguen entregar el 63% del valor estimado de partida. Esta circunstancia se repite de forma sistemática ejercicio tras ejercicio. Las expectativas de generación de valor son significativamente mayores que las reales y año tras año se aprecia una mejoría progresiva pero leve que no se apoya en el valor esperado, sino en una fracción de dicho valor, dando lugar a un fenómeno conocido como “persiana veneciana”.
Sin ser exhaustivos, existen diversas razones por las que tradicionalmente la inversión en transformación digital de las operaciones falla:
- Pilotos sin escalar. Inversión de capital y esfuerzo en una sucesión de pilotos que luego rara vez se escalan.
- Silos estancos. Reticencia a superar los silos departamentales y a aplicar soluciones transversales.
- Objetivos equivocados. Foco en casos de uso centrados en tecnología más que en solucionar los problemas del “core” o en crear nuevos modelos de negocio.
- Desconexión de la estrategia digital de la excelencia operativa.
- Falta de visión transversal. Tendencia a considerar “Digital como IT 2.0” y no como una transformación global que debe impactar e involucrar a toda la compañía.
- Cultura corporativa. Problemas para alinear el talento y la cultura de las empresas con los retos planteados.
La solución: una transformación digital inteligente de las operaciones
Para superar los problemas anteriores y transformar de forma radical y a escala la productividad industrial, es necesario adoptar una estrategia de transformación digital basada en tres pilares fundamentales:
1. Una metodología de mejora continua y gestión del cambio escalable y digitalizada como columna vertebral de la transformación. Un hecho sorprendente y frecuente en las empresas es la disociación entre los esfuerzos de mejora continua de tipo Lean, Six Sigma o TQM respecto de los esfuerzos de transformación digital o de los de gestión de personas. Esta disociación, heredera de la típica actuación por silos departamentales, ha llevado en muchas ocasiones a que todos estos esfuerzos individuales no hayan tenido éxito.
Los esfuerzos en Lean Six Sigma, por ejemplo, se suelen asociar al departamento de fabricación y raramente se trasladan a otras áreas. Es frecuente encontrar dificultades para escalar este esfuerzo de forma organizada de un nivel planta a corporativo. Del mismo modo las acciones de mejora se diluyen en el tiempo debido a varias causas como cambios organizativos, rotación de personas, falta de digitalización, falta de soporte directivo, etc.
Por otra parte, en muchas ocasiones se asocia la transformación digital a una evolución de la función de IT, en lugar de considerarla como un cambio fundamental de la forma en la que se hacen las cosas que debe alcanzar a todas las áreas de la compañía. Igualmente, durante años se ha asociado lo digital al eje de relación con clientes y ventas y no con las operaciones productivas. Hoy sigue siendo complicado encontrar formación en Transformación Digital con contenido de operaciones. En definitiva, hay vida más allá de la web.
Las compañías líderes que están consiguiendo resultados excelentes en su transformación emplean una metodología robusta de mejora continua, soportada por herramientas digitales que permiten:
- Identificar un punto de partida y objetivos en base a unos niveles de madurez que correlacionen las prácticas operativas a implantar con la consecución de unos indicadores medibles con impacto financiero.
- Establecer acciones de mejora con una granularidad que va desde el nivel de línea hasta corporativo, pasando por planta y región.
- Asignar las acciones a personas concretas y seguir su ejecución de forma digital.
- Reforzar y otorgar responsabilidad al operario sobre la mejora continua.
- No reinventar la rueda. Muchas compañías han realizado ya un esfuerzo exitoso de digitalización. Apoyarse en conocimiento probado permite saltarse etapas en el camino y no tropezar donde otros lo han hecho.
- Escalar y sostener la transformación en el tiempo independientemente de cambios organizacionales y rotación de personas. El conocimiento es del individuo…y de la empresa.
- Aportar herramientas y formación en el día a día para que operarios y mandos puedan cumplir con las acciones asignadas.
- Identificación objetiva de las principales pérdidas.
- Analítica avanzada de pérdidas.
- Eliminación permanente de las pérdidas.
- Gestión estructurada del día a día en la planta.
- Reducción de costes, mejora de la calidad y aumento de la productividad.
- IoT & MES para la captura de datos de planta en tiempo real y sin sesgos de usuario.
- Integración de datos del ERP (planificación de recursos empresariales) a pie de planta: órdenes de trabajo, planificación, existencias, costes, etc.
- Visión integrada de la información, contextualizando información de planta con la del ERP. El cálculo de indicadores debe ser consistente para poder comparar “peras con peras” a nivel de planta y de compañía.
- Analítica causal de las pérdidas para eliminarlas de forma permanente.
- Herramientas de colaboración con movilidad multidispositivo que soporten tanto la actividad individual del operario como todas las reuniones de planta (coordinación diaria, cambio de turno, etc.).
- +15% en el OEE.
- +20% en la capacidad de producción.
- -35% en pérdida de tiempo de producción no planificada.
- 25%-40% reducción de costes, principalmente energía, mantenimiento, logística y mermas.
- 45%-85% mejora en la involucración del empleado.
- Reducción de mermas en equipos.
- Aplicación rápida y automática de garantías de equipos.
- Mejora de la disponibilidad de materiales en campo o en tienda.
- Reducción del circulante.
- Aceleración de la activación de instalaciones.
- Aceleración del despliegue de proyectos de CAPEX.
- Reducción del esfuerzo de gestión de contratos con subcontratistas.
- Metodología de mejora continua y gestión del cambio.
- Digitalización de las operaciones del día a día en planta.
- Aplicación de tecnologías emergentes de forma combinada.
Por ejemplo, P&G ha desarrollado una metodología que aplica de forma consistente en todas sus plantas y compañías que adquiere. Esta metodología está soportada por una solución digital en la nube que permite diagnosticar, planificar, ejecutar y sostener planes de mejora continua en el tiempo.
Esta metodología establece una serie de niveles de madurez asociados y explica cómo ir evolucionando de nivel en nivel a partir de un estadio inicial de forma sistemática. La aplicación de esta metodología ha permitido a P&G que la práctica totalidad de sus plantas cuenten con niveles de productividad (medida como OEE Overall Equipment Efficiency) superiores al 90%.
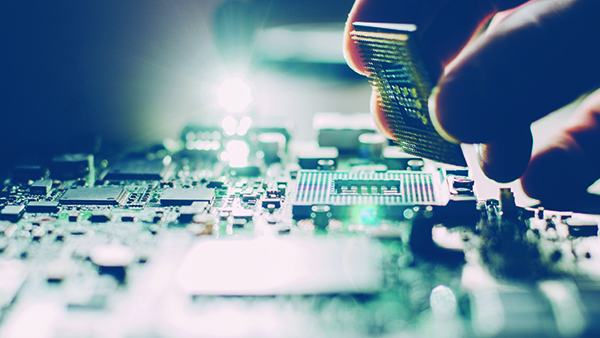
“La competitividad de la externalización se está reduciendo. el salario medio en china prácticamente se ha triplicado en los últimos 10 años”.
2. Foco en la digitalización del día a día de las operaciones en planta.
El segundo aspecto clave consiste en focalizarse en el núcleo de oportunidad para la industria manufacturera: las operaciones del día a día en planta.
Hay compañías que se “suben al carro” de la Industria 4.0 realizando pequeñas actuaciones con nuevas tecnologías en puntos aislados de su cadena de valor antes de haber solucionado su día a día en planta. Estas compañías se lanzan a inversiones relevantes en tecnología que en ocasiones no resuelven los factores que impactan de forma radical en el rendimiento en planta:
La clave de la digitalización de este core está en integrar la capa de negocio planificadora y ejecutiva con el nivel operador o de planta para sincronizar las operaciones y reducir al mínimo actividades y tiempos de no valor.
A nivel tecnológico esta integración implica eliminar el papel y la manualidad del día a día de planta y sustituirlo por herramientas digitales basadas en:
EY, por ejemplo, ha desarrollado el enfoque Smartfactory que integra una metodología avanzada de mejora continua con una solución digital que permite a las compañías la gestión sistemática de toda la operativa en planta, tanto en su día a día como en la toma de control de compañías adquiridas.
Smartfactory integra la información de gestión con los datos de planta y mediante diferentes apps permite gestionar la ejecución de órdenes de producción, el mantenimiento, el calibrado de equipos, la identificación de pérdidas y la coordinación de todas las reuniones de planta en un entorno paperless. Este modelo se acompaña de una transformación cultural donde se le otorga responsabilidad y ownership al operario en su entorno de actuación.
Smartfactory ha sido implantado en numerosas compañías de sectores diversos como alimentación, bebidas, industrial, automoción o farmacéutico con resultados muy relevantes y sostenidos en el tiempo:
Fuente: EY Smartfactory eBook
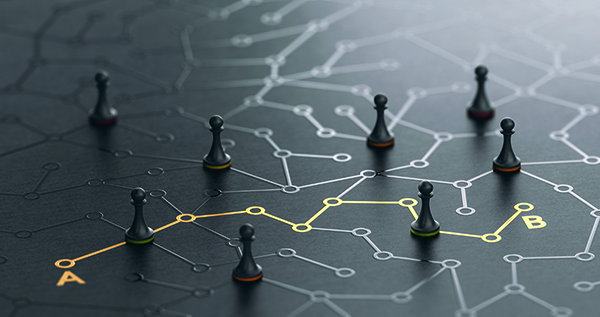
“Corea del Sur cuenta con 868 robots por cada 10.000 habitantes, Alemania con 363 y España con 191, menos de un 25% que Corea”.
3. Aplicación de tecnologías emergentes de forma combinada en base a casos de uso con un retorno claro.
Finalmente, y de forma complementaria a lo anterior, la aplicación práctica de Industria 4.0 debe contemplar el uso selectivo de tecnologías que respondan a retos de partes específicas de la cadena de valor, dando lugar a casos de uso autosostenibles.
Al contrario que revoluciones industriales anteriores, la Industria 4.0 no se basa en una sola tecnología, sino en la combinación de varias que van llegando a la industria en forma de oleadas.
Por ejemplo, según datos de Stratasys, Unilever ha integrado el uso de fabricación aditiva o 3D Printing en sus procesos industriales reduciendo el tiempo de prototipado de nuevos productos en un 40%, aplicando tecnología a la fabricación de los moldes, uno de los principales cuellos de botella en el desarrollo de nuevos productos.
Blockchain es otra tecnología que está generando valor a lo largo de la cadena de suministro, basándose en la visibilidad y trazabilidad que ofrece. Por ejemplo, una empresa del sector de telecomunicaciones ha aplicado esta tecnología conectando toda la cadena desde la fabricación de componentes hasta el cliente final, impactando en la cuenta de pérdidas y ganancias a través de:
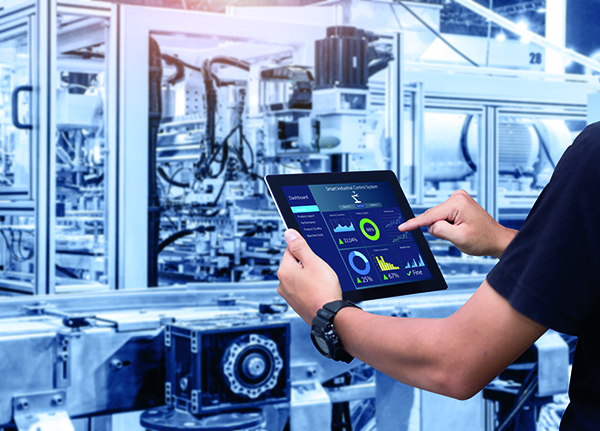
“Equipamiento eléctrico, maquinaria, equipamiento de transporte, electrónica de consumo, químico y farmacéutico son los sectores más propensos a la relocalización”.
Conclusión
Disponer de una capacidad productiva moderna y eficiente es necesario y beneficioso para el mercado europeo. Aumenta la resiliencia ante cortes de suministro, proporciona a los clientes apreciados productos locales y tiene un impacto positivo en el empleo de calidad y la economía regional.
Para disponer de esta capacidad la clave es una digitalización inteligente de las operaciones de planta, que se focalice en el core y que se apalanque en enfoques y activos probados orientados a una mejora continua sostenible y escalable.
Esta transformación solo tendrá éxito si integra de forma metodológica el factor humano, teniendo en cuenta las particularidades demográficas, educacionales y culturales de las personas.
Aquellas compañías que están navegando este proceso con éxito están logrando un retorno superior para sus accionistas y además están teniendo un impacto positivo en su comunidad.
España, así como el resto de la UE, apuestan por el sector industrial y por ello el 23% (la mayor partida) del Presupuesto del Plan de Resiliencia está dedicada a la Modernización y digitalización del tejido industrial y de la PYME, recuperación del turismo e impulso a una España Nación Emprendedora. Asimismo, el 11% estará dedicado a Educación y conocimiento, formación continua y desarrollo de capacidades.
Con el plan de ayuda, el sector manufacturero tiene una bala de plata para conseguir sus objetivos. Una bala que no se puede desperdiciar en actuaciones incrementales que den lugar a un impacto menor en sus estados financieros. Las compañías deben actuar de forma decidida y asumir que deben transformarse actuando sobre el núcleo de sus operaciones. El reto está servido.