Actualidad/ Noticias
AECOCINFO | AECOC celebra la segunda edición del ‘After Work Lean Logistics
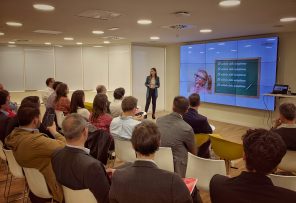
AECOC celebró, en su sede de Madrid, la segunda edición del ‘After Work Lean Logistics’, que reunió a más de 50 profesionales de la logística para analizar las estrategias de mejora continua que tres empresas líderes del gran consumo y de la logística aplican en sus cadenas de suministros para ser más eficientes, flexibles y productivos en sus operaciones logísticas.
La responsable de eficiencia productiva de Entrepinares, Ana Benito, expuso los cinco pilares del sistema de mejora continua que la empresa ha bautizado como Entrepinares Production System: comunicación, indicadores, herramientas de implicación de personal, estandarización, mejora de la productividad y liderazgo.
La metodología, aplicada en seis de las plantas de la compañía líder en España en la fabricación de quesos y derivados lácteos, fomenta las reuniones en las que se plantean, evalúan, priorizan y estandarizan las ideas de mejora; recurre a los indicadores para identificar debilidades y fortalezas e impulsa talleres de mejora para afinar las ideas seleccionarlas y adaptarlas a las necesidades operativas. “La implantación del Lean no es algo que empiece y acabe, sino que debe tratarse como una transformación cultural si el objetivo es que sea duradera y sostenible. Para nosotros, trabajar con Lean ha supuesto todo un cambio cultural”, resume Benito.
Bajo estos principios, Entrepinares ha invertido más de 1.000 horas de formación en su programa Lean, que han resultado en más de 5.200 ideas de mejora generadas y más de 700 propuestas analizadas y llevadas a cabo.
Por otra parte, los proyectos de Lean Logistics de Unide y Arvato que se presentaron en la jornada son resultado de la experiencia de ambas empresas en la pasada edición del programa ‘Lean Logistics Management en Gran Consumo’ de AECOC.
La cooperativa de supermercados, Unide, se marcó como objetivo de mejora reducir las segundas vueltas en la preparación de sus pedidos del servicio cash&carry para mejorar en costes y productividad. Según detalló el director de logística de la sociedad, José Manuel Souto, el método Lean se tradujo en un plan de acción basado en siete etapas, que iban desde el análisis de la situación a mejorar, a la fijación de los objetivos de mejora, la propuesta de acciones a aplicar y, finalmente, el seguimiento de los resultados.
“En un mes pasamos de un promedio semanal de 289 segundas vueltas en la preparación de pedidos a menos de 180, lo que tuvo un impacto en la productividad de los preparadores y el promedio mensual de cajas que podíamos preparar por jornada”, explica Souto.
El ingeniero de logística de Arvato, Javier Sierra, cerró la jornada explicando el proyecto de mejora continua del operador logístico, que gestiona los envíos de más de 200 tiendas online en todo el mundo y cuenta con una plantilla de más de 15.000 trabajadores.
Tras su paso por la formación de AECOC, Arvato decidió centrar su proceso de mejora continua en la fase de control de calidad, o clearing, de su logística. “El crecimiento de los pedidos colapsaba esta etapa del proceso y generaba errores que suponían un sobrecoste superior a los 21.000 euros anuales dedicados a la corrección de errores”, expone Sierra.
Tras esta exposición de la situación de partida, Arvato creó un mapa detallado de su proceso logístico y se apoyó en el análisis de datos para detectar las causas de los errores generados, buscar sistemas para neutralizarlos y marcarse objetivos de mejora. El inicio del proyecto Lean ha supuesto, en pocos meses, que Arvato haya reducido el porcentaje de paquetes revisados del 12,5% a 4,6%, con una consecuente caída a más de la mitad de las horas semanales dedicadas a la corrección de errores. “Nuestra previsión es que los indicadores sean aún más positivos con el paso de los meses”, aventura el responsable de Arvato.
Nuevo programa Lean Logistics Management
La jornada ‘After Work Lean Logistic’ fue el preámbulo de la próxima edición del programa formativo ‘Lean Logistics Management en Gran Consumo’, que AECOC iniciará el próximo 17 de marzo.
La formación combinará sesiones teóricas dedicadas a analizar las claves del método Lean de mejora continua aplicado a los procesos logísticos con talleres y sesiones prácticas a cargo de los especialistas de AECOC y de empresas referentes en este sistema de gestión, como Eroski y Entrepinares, que descubrirán a los participantes qué estrategias han aplicado para eliminar las fases más ineficientes de su cadena de suministro.
Según los datos de la asociación, los procesos de logística y transporte pueden representar entre el 7% y el 30% del coste de un producto, y hasta el 50% de este coste puede venir de actividades que no aportan un valor añadido al proceso, por lo que la mejora de estos procesos es clave para garantizar la competitividad de las compañías.
Además, las empresas que no aplican sistemas de mejora continua en sus operaciones logísticas pierden entre el 10% y el 30% de sus clientes cada año. El nuevo programa de AECOC ofrecerá las claves para mejorar la eficiencia, la flexibilidad y la productividad en las operaciones logísticas destinadas del Gran Consumo y, además, los participantes obtendrán la certificación Green Belt, que garantiza la optimización de los procesos en una organización.